Optimale Nutzung von Industrie 4.0-Investitionen mit Wireless Power
Da Industrie 4.0 in vollem Gange ist, verstärken viele Unternehmen den Einsatz fortschrittlicher Technologien wie künstliche Intelligenz, Internet der Dinge (IoT), 5G-Konnektivität, Sensoren und Robotik. Aus gutem Grund. Laut einer Studie von Deloitte aus dem Jahr 2020 übertreffen Unternehmen mit umfassenden Industrie-4.0-Strategien ihre Mitbewerber ohne oder mit disjunkten Strategien deutlich.
Rund 90 % der befragten Unternehmen mit umfassenden Industrie-4.0-Strategien erzielten im letzten Jahr ein jährliches Umsatzwachstum von mindestens 5 %.
Analysten von Mkinsey & Company sagen, dass es nicht ungewöhnlich ist, Maschinenausfallzeiten um 30 bis 50 % zu reduzieren, den Durchsatz um 10 bis 30 % zu steigern, Verbesserungen um 15 bis 50 %, 30 % höhere Arbeitsproduktivität und 85 % genauere Prognosen dank der Digitalisierung zu verzeichnen. Fabriken.
Die Grenzen von Kabeln und BatterienViele der heutigen Industrie-4.0-Technologien zeichnen sich durch komplexe, teure, umständliche und manchmal gefährliche Verkabelungs- und Verbindungslösungen aus. Beispielsweise werden Cobots und autonome mobile Roboter und Fahrzeuge (AMR und AMV) in der Regel von hocheffizienten Batterien oder mit Kabeln und Netzkabeln betrieben.
Über 60 % der Einrichtungskosten für Industrial IoT (IIoT) werden für Verkabelung und Installation ausgegeben. Auch das regelmäßige Aufladen oder Austauschen von Batterien kann die Opportunitätskosten schnell erhöhen. Ein Gerät, das Strom verliert, kann eine Kettenreaktion auslösen, die die Produktivität der gesamten Fabrik beeinträchtigt. Ganz zu schweigen davon, dass das Identifizieren und Ersetzen leerer Batterien in einer Produktionsanlage ein logistischer Albtraum ist.
Außerdem stellt sich die Frage der Sicherheit, da beschädigte Lithium-Ionen-Akkus ein erhebliches Brandrisiko darstellen. Schäden können sofort oder über einen längeren Zeitraum durch physische Einwirkung, Einwirkung bestimmter Temperaturen und unsachgemäßes Aufladen auftreten.
Die Alternative ist leider nicht viel besser: Freiliegende Kabel und Buchsen sind auch in Industrieumgebungen besonders gefährlich. Darüber hinaus sind Industrie 4.0-Technologien per Definition dazu gedacht, sich zu vernetzen und Daten auszutauschen. Daher benötigen sie ausreichend Leistung und müssen Daten jederzeit schnell und reibungslos übertragen können.
Batterien bieten diese Fähigkeit einfach nicht. Es macht keinen Sinn, ein batteriebetriebenes Gerät an ein Kabel anzuschließen, um eine 24-Stunden-Datenübertragung zu ermöglichen.
Automatisierung verlangt drahtlose FreiheitMit dem Aufkommen der industriellen Automatisierung in den letzten Jahrzehnten stellt es ein erhebliches Problem dar, eine Reihe von Maschinen zu haben, die enorme Mengen an Strom und Datenübertragung benötigen. Glücklicherweise hat sich die drahtlose Energie zusammen mit der magnetischen Induktion weiterentwickelt, um sowohl kontaktlose Energie als auch Datenübertragung zu ermöglichen, was ideal für Industrie 4.0-Technologien ist, die Batterielebensdauer und Zuverlässigkeit erfordern. /p>
Industrieroboter und Drohnen müssen in der Lage sein, ihre Aufgabe autonom zu erledigen und sich schnell wieder aufzuladen. Die fortschrittliche kabellose Ladetechnologie vereinfacht den Andockvorgang erheblich, indem sie eine starke Fehlausrichtung zulässt, sodass Roboter einfach zu einem kabellosen Ladepad rollen und sich aufladen können.
Darüber hinaus nehmen kabellose Ladegeräte in einer Fabrikumgebung nur minimalen Platz ein und ermöglichen es Robotern sogar, "unterwegs" zu verschiedenen festen Zeiten in ihrem Betrieb aufzuladen, z. B. beim Laden, Anstehen, Warten usw. Diese Innovation eliminiert die Notwendigkeit menschlicher Eingriffe, was bedeutet, dass sich die Mitarbeiter auf Aufgaben mit höherer Priorität oder sehr komplexe und teure Kontaktladestationen konzentrieren können.
Batteriemanagement und GerätesicherheitWLAN kann die Effizienz steigern, indem es eine bessere Akkusteuerung ermöglicht. Batterieladeprozesse können optimiert und überwacht werden, um sicherzustellen, dass jedes Gerät unter optimalen Bedingungen geladen wird, einschließlich Spannung, Strom und Zeit.
Dies verlängert die Batterielebensdauer und erspart kostspielige Austauschvorgänge. Darüber hinaus müssen sich Robotik-Anwender dank des kabellosen Ladens keine Sorgen über Betriebsunterbrechungen aufgrund von Robotern machen, die nicht richtig laden oder fehlerhafte Teile, wodurch sie bessere Produktivitätssteigerungen erzielen können, ohne unerwartete Kosten zu verursachen.
Die kabellose Stromversorgung ist auch sicherer, da Pogo-Stifte und andere Komponenten eliminiert werden, die mit herkömmlichen galvanisierten Verbindungen verbunden sind, die anfällig für elektrische Funken, Korrosion und andere Gefahren sind, die Brände verursachen können. Darüber hinaus beinhalten viele industrielle Anwendungsfälle dynamische oder Außenumgebungen, zum Beispiel ...

Da Industrie 4.0 in vollem Gange ist, verstärken viele Unternehmen den Einsatz fortschrittlicher Technologien wie künstliche Intelligenz, Internet der Dinge (IoT), 5G-Konnektivität, Sensoren und Robotik. Aus gutem Grund. Laut einer Studie von Deloitte aus dem Jahr 2020 übertreffen Unternehmen mit umfassenden Industrie-4.0-Strategien ihre Mitbewerber ohne oder mit disjunkten Strategien deutlich.
Rund 90 % der befragten Unternehmen mit umfassenden Industrie-4.0-Strategien erzielten im letzten Jahr ein jährliches Umsatzwachstum von mindestens 5 %.
Analysten von Mkinsey & Company sagen, dass es nicht ungewöhnlich ist, Maschinenausfallzeiten um 30 bis 50 % zu reduzieren, den Durchsatz um 10 bis 30 % zu steigern, Verbesserungen um 15 bis 50 %, 30 % höhere Arbeitsproduktivität und 85 % genauere Prognosen dank der Digitalisierung zu verzeichnen. Fabriken.
Die Grenzen von Kabeln und BatterienViele der heutigen Industrie-4.0-Technologien zeichnen sich durch komplexe, teure, umständliche und manchmal gefährliche Verkabelungs- und Verbindungslösungen aus. Beispielsweise werden Cobots und autonome mobile Roboter und Fahrzeuge (AMR und AMV) in der Regel von hocheffizienten Batterien oder mit Kabeln und Netzkabeln betrieben.
Über 60 % der Einrichtungskosten für Industrial IoT (IIoT) werden für Verkabelung und Installation ausgegeben. Auch das regelmäßige Aufladen oder Austauschen von Batterien kann die Opportunitätskosten schnell erhöhen. Ein Gerät, das Strom verliert, kann eine Kettenreaktion auslösen, die die Produktivität der gesamten Fabrik beeinträchtigt. Ganz zu schweigen davon, dass das Identifizieren und Ersetzen leerer Batterien in einer Produktionsanlage ein logistischer Albtraum ist.
Außerdem stellt sich die Frage der Sicherheit, da beschädigte Lithium-Ionen-Akkus ein erhebliches Brandrisiko darstellen. Schäden können sofort oder über einen längeren Zeitraum durch physische Einwirkung, Einwirkung bestimmter Temperaturen und unsachgemäßes Aufladen auftreten.
Die Alternative ist leider nicht viel besser: Freiliegende Kabel und Buchsen sind auch in Industrieumgebungen besonders gefährlich. Darüber hinaus sind Industrie 4.0-Technologien per Definition dazu gedacht, sich zu vernetzen und Daten auszutauschen. Daher benötigen sie ausreichend Leistung und müssen Daten jederzeit schnell und reibungslos übertragen können.
Batterien bieten diese Fähigkeit einfach nicht. Es macht keinen Sinn, ein batteriebetriebenes Gerät an ein Kabel anzuschließen, um eine 24-Stunden-Datenübertragung zu ermöglichen.
Automatisierung verlangt drahtlose FreiheitMit dem Aufkommen der industriellen Automatisierung in den letzten Jahrzehnten stellt es ein erhebliches Problem dar, eine Reihe von Maschinen zu haben, die enorme Mengen an Strom und Datenübertragung benötigen. Glücklicherweise hat sich die drahtlose Energie zusammen mit der magnetischen Induktion weiterentwickelt, um sowohl kontaktlose Energie als auch Datenübertragung zu ermöglichen, was ideal für Industrie 4.0-Technologien ist, die Batterielebensdauer und Zuverlässigkeit erfordern. /p>
Industrieroboter und Drohnen müssen in der Lage sein, ihre Aufgabe autonom zu erledigen und sich schnell wieder aufzuladen. Die fortschrittliche kabellose Ladetechnologie vereinfacht den Andockvorgang erheblich, indem sie eine starke Fehlausrichtung zulässt, sodass Roboter einfach zu einem kabellosen Ladepad rollen und sich aufladen können.
Darüber hinaus nehmen kabellose Ladegeräte in einer Fabrikumgebung nur minimalen Platz ein und ermöglichen es Robotern sogar, "unterwegs" zu verschiedenen festen Zeiten in ihrem Betrieb aufzuladen, z. B. beim Laden, Anstehen, Warten usw. Diese Innovation eliminiert die Notwendigkeit menschlicher Eingriffe, was bedeutet, dass sich die Mitarbeiter auf Aufgaben mit höherer Priorität oder sehr komplexe und teure Kontaktladestationen konzentrieren können.
Batteriemanagement und GerätesicherheitWLAN kann die Effizienz steigern, indem es eine bessere Akkusteuerung ermöglicht. Batterieladeprozesse können optimiert und überwacht werden, um sicherzustellen, dass jedes Gerät unter optimalen Bedingungen geladen wird, einschließlich Spannung, Strom und Zeit.
Dies verlängert die Batterielebensdauer und erspart kostspielige Austauschvorgänge. Darüber hinaus müssen sich Robotik-Anwender dank des kabellosen Ladens keine Sorgen über Betriebsunterbrechungen aufgrund von Robotern machen, die nicht richtig laden oder fehlerhafte Teile, wodurch sie bessere Produktivitätssteigerungen erzielen können, ohne unerwartete Kosten zu verursachen.
Die kabellose Stromversorgung ist auch sicherer, da Pogo-Stifte und andere Komponenten eliminiert werden, die mit herkömmlichen galvanisierten Verbindungen verbunden sind, die anfällig für elektrische Funken, Korrosion und andere Gefahren sind, die Brände verursachen können. Darüber hinaus beinhalten viele industrielle Anwendungsfälle dynamische oder Außenumgebungen, zum Beispiel ...
What's Your Reaction?
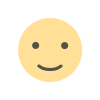
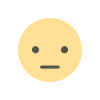
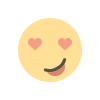
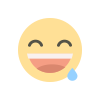
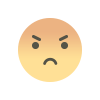
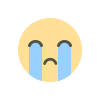
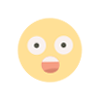