Optimization of an RC tilt-rotor VTOL
There are a variety of possible motor configurations to choose from when building a fixed-wing VTOL drone, but few take the twin-motor tilt-rotor approach used by the V-22 Osprey. However, it remains a popular DIY drone for military aircraft fans, like [Tom Stanton]. He recently built his 5th tiltrotor VTOL and gave great insight into the development process. Video after the break.
The key components of any small scale tiltrotor are the tilt mechanism and the flight controller. [Tom's] tilt mechanism uses a high-speed, high-torque servo that spins the motor mount via a 3D-printed gear mechanism. This means that the servo does not need to carry the full motor load and the gearing can be optimized for torque and speed. [Tom] also used the pitch motors for yaw and roll control during forward flight, allowing him to eliminate all other conventional control surfaces except elevator.
>The flight controller consists of a Teensy module and gyroscope/accelerometer, and runs dRehmFlight flight stabilization firmware. dRehmflight was specifically created to be easily adapted to a wide variety of experimental aircraft configurations, and it got [Tom] airborne on the first attempt.
Carbon fiber tubes are used for the wing spars and tail boom, and are bolted to a fuselage made up of 3D printed brackets and 1mm fiberglass reinforced plastic sheet . [Tom] chose a NACA 4412 airfoil wing for its linear coefficient of lift over a wide angle of attack range, allowing for a smooth transition between hover and forward flight. The wing was 3D printed with lightweight foaming PLA (LW-PLA), which required careful design for a quality print. The foaming of LW-PLA means it will always ooze if it stops extruding, so [Tom] designed the wing surface and internal ribs to extrude in a continuous line using the "vase mode" of the slicer. Had some issues with the matte black fenders starting to warp in the sun, which was resolved by reprinting the fenders in white.
The plane performed well in both flight modes, but had trouble slowing down when transitioning to hover. This is a major improvement over the previous version, which lacked yaw control in the hover and was a little unstable in forward flight.
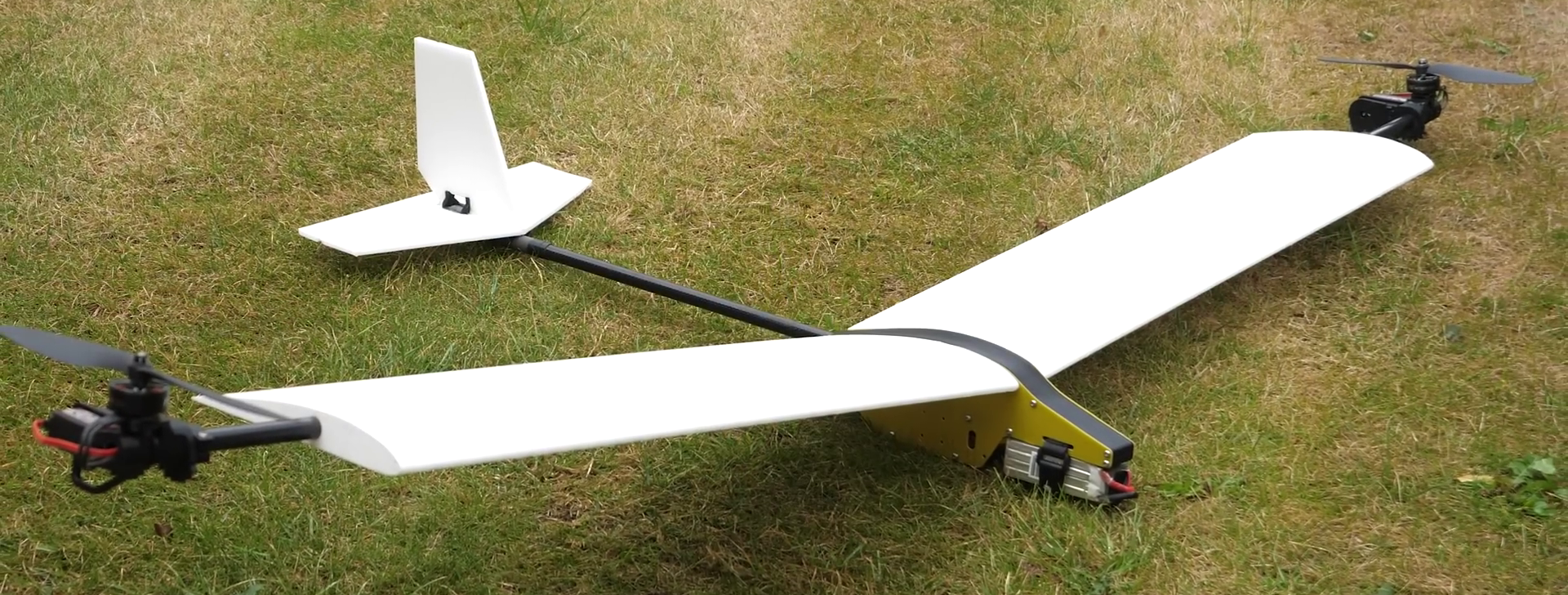
There are a variety of possible motor configurations to choose from when building a fixed-wing VTOL drone, but few take the twin-motor tilt-rotor approach used by the V-22 Osprey. However, it remains a popular DIY drone for military aircraft fans, like [Tom Stanton]. He recently built his 5th tiltrotor VTOL and gave great insight into the development process. Video after the break.
The key components of any small scale tiltrotor are the tilt mechanism and the flight controller. [Tom's] tilt mechanism uses a high-speed, high-torque servo that spins the motor mount via a 3D-printed gear mechanism. This means that the servo does not need to carry the full motor load and the gearing can be optimized for torque and speed. [Tom] also used the pitch motors for yaw and roll control during forward flight, allowing him to eliminate all other conventional control surfaces except elevator.
>The flight controller consists of a Teensy module and gyroscope/accelerometer, and runs dRehmFlight flight stabilization firmware. dRehmflight was specifically created to be easily adapted to a wide variety of experimental aircraft configurations, and it got [Tom] airborne on the first attempt.
Carbon fiber tubes are used for the wing spars and tail boom, and are bolted to a fuselage made up of 3D printed brackets and 1mm fiberglass reinforced plastic sheet . [Tom] chose a NACA 4412 airfoil wing for its linear coefficient of lift over a wide angle of attack range, allowing for a smooth transition between hover and forward flight. The wing was 3D printed with lightweight foaming PLA (LW-PLA), which required careful design for a quality print. The foaming of LW-PLA means it will always ooze if it stops extruding, so [Tom] designed the wing surface and internal ribs to extrude in a continuous line using the "vase mode" of the slicer. Had some issues with the matte black fenders starting to warp in the sun, which was resolved by reprinting the fenders in white.
The plane performed well in both flight modes, but had trouble slowing down when transitioning to hover. This is a major improvement over the previous version, which lacked yaw control in the hover and was a little unstable in forward flight.
What's Your Reaction?
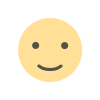
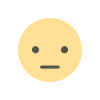
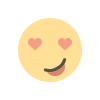
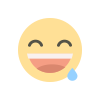
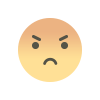
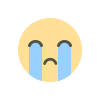
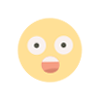